Polymeric field synergy principle: Revealing the intrinsic mechanism of screw channel optimization to enhance thermal management and process efficiency
DOI:
https://doi.org/10.18686/cest.v2i2.134Keywords:
polymer extrusion; mixing efficiency; heat and mass transport efficiency; energy utilization efficiency; field synergy principleAbstract
The process efficiency and energy efficiency of extrusion equipment emerge as pivotal challenges constraining the development of the polymer extrusion industry. This article presents a new principle of polymeric field synergy to guide the solution to the low mixing efficiency and energy utilization efficiency of traditional extrusion equipment. Finite element analysis was conducted on four novel unconventional screw configurations and compared with the traditional single-thread screw. Results revealed that more complicated melt flow patterns generated in the modified novel screw configurations enhanced the stretching deformation or helical flow. The stretching or helical flows to varying degrees during the melt extrusion process thereby improved the mixing and heat transport efficiency. Among them, helical flow induced by the Maddock element exhibited the most significant impact on stretching flow and ductile deformation in the flow field. Simultaneously, the helical flow caused radial motion of the internal material, significantly promoting the synergy between the velocity field, velocity gradient field, and temperature gradient field. This enhanced radial heat and mass transport efficiency within the screw channel, subsequently improving the overall operational efficiency of the equipment. The results of the finite element analysis have substantiated the scientific validity of the polymeric field synergy principle.
References
1. Dong H, Liu Y, Zhao Z, et al. Carbon neutrality commitment for China: from vision to action. Sustainability Science. 2022; 17(5): 1741-1755. doi: 10.1007/s11625-022-01094-2 DOI: https://doi.org/10.1007/s11625-022-01094-2
2. Dong H, Xue M, Xiao Y, et al. Do carbon emissions impact the health of residents? Considering China’s industrialization and urbanization. Science of The Total Environment. 2021; 758: 143688. doi: 10.1016/j.scitotenv.2020.143688 DOI: https://doi.org/10.1016/j.scitotenv.2020.143688
3. Yu S, Xiang H, Zhou J, et al. Typical polymer fiber materials: An overview and outlook. Acta Polymerica Sinica. 2020; 51(1): 39-54. doi:10.11777/j.issn1000-3304.2020.19148
4. Li W, Liu Q, Zhang Y, et al. Biodegradable Materials and Green Processing for Green Electronics. Advanced Materials. 2020; 32(33). doi: 10.1002/adma.202001591 DOI: https://doi.org/10.1002/adma.202001591
5. Abeykoon C, Kelly AL, Vera-Sorroche J, et al. Process efficiency in polymer extrusion: Correlation between the energy demand and melt thermal stability. Applied Energy. 2014; 135: 560-571. doi: 10.1016/j.apenergy.2014.08.086 DOI: https://doi.org/10.1016/j.apenergy.2014.08.086
6. Deng J, Li K, Harkin-Jones E, et al. Energy monitoring and quality control of a single screw extruder. Applied Energy. 2014; 113: 1775-1785. doi: 10.1016/j.apenergy.2013.08.084 DOI: https://doi.org/10.1016/j.apenergy.2013.08.084
7. Dray RF. How to compare barrier screws. Plastics Technology. 2002; 48(12): 46-49, 59. DOI: https://doi.org/10.1016/S0034-3617(02)80228-4
8. Chen J, Dai P, Yao H, et al. Numerical analysis of mixing performance of mixing section in pin-barrel single-screw extruder. Journal of Polymer Engineering. 2011; 31(1): 53-62. doi: 10.1515/polyeng.2011.009 DOI: https://doi.org/10.1515/polyeng.2011.009
9. Liu T, Du Y, He X. Statistical research on the mixing properties of wave based screws by numerical simulations. International Polymer Processing. 2023; 38(2): 200-213. doi: 10.1515/ipp-2022-4253 DOI: https://doi.org/10.1515/ipp-2022-4253
10. Spalding MA, Sun X, Kodjie SL, et al. A maddock mixer design that mitigates gels in polyethylene resin film applications. Journal of Plastic Film & Sheeting. 2022; 39(2): 174-189. doi: 10.1177/87560879221124172 DOI: https://doi.org/10.1177/87560879221124172
11. Formela K, Cysewska M, Haponiuk J. The influence of screw configuration and screw speed of co-rotating twin screw extruder on the properties of products obtained by thermomechanical reclaiming of ground tire rubber. Polimery. 2014; 59(02): 170-177. doi: 10.14314/polimery.2014.170 DOI: https://doi.org/10.14314/polimery.2014.170
12. Jian R, Dai R, Sain M, et al. Ductile behavior and heat transfer efficiency in polymer extrusion by self-controlled “flipping melt-pancakes” with multi-fields synergy. International Journal of Heat and Mass Transfer. 2022; 186: 122517. doi: 10.1016/j.ijheatmasstransfer.2021.122517 DOI: https://doi.org/10.1016/j.ijheatmasstransfer.2021.122517
13. Jian R, Dai R, Sain M, et al. A strategy of stretching melt to a thin layer: Self-controlled “stretching melt-pancakes” to enhance heat transfer and mixing during polymer extrusion. Applied Thermal Engineering. 2023; 224: 120090. doi: 10.1016/j.applthermaleng.2023.120090 DOI: https://doi.org/10.1016/j.applthermaleng.2023.120090
14. Abeykoon C, Pérez P, Kelly AL. The effect of materials’ rheology on process energy consumption and melt thermal quality in polymer extrusion. Polymer Engineering & Science. 2020; 60(6): 1244-1265. doi: 10.1002/pen.25377 DOI: https://doi.org/10.1002/pen.25377
15. Jian R, Yang W, Xie P, et al. Enhancing a multi-field-synergy process for polymer composite plasticization: A novel design concept for screw to facilitate phase-to-phase thermal and molecular mobility. Applied Thermal Engineering. 2020; 164: 114448. doi: 10.1016/j.applthermaleng.2019.114448 DOI: https://doi.org/10.1016/j.applthermaleng.2019.114448
16. Jian R, Shi Z, Liu H, et al. Enhancing Mixing and Thermal Management of Recycled Carbon Composite Systems by Torsion-Induced Phase-to-Phase Thermal and Molecular Mobility. Polymers. 2020; 12(4): 771. doi: 10.3390/polym12040771 DOI: https://doi.org/10.3390/polym12040771
17. Jian R, Xie P, Liu H, et al. Ductile forming of polymers by inducing torsional flow to enhance heat transfer and mixing. Journal of Materials Processing Technology. 2020; 283: 116715. doi: 10.1016/j.jmatprotec.2020.116715 DOI: https://doi.org/10.1016/j.jmatprotec.2020.116715
18. Jian R, Yang W, Cheng L, et al. Numerical analysis of enhanced heat transfer by incorporating torsion elements in the homogenizing section of polymer plasticization with the field synergy principle. International Journal of Heat and Mass Transfer. 2017; 115: 946-953. doi: 10.1016/j.ijheatmasstransfer.2017.07.121 DOI: https://doi.org/10.1016/j.ijheatmasstransfer.2017.07.121
19. Dhakal P, Das SR, Poudyal H, et al. Numerical simulations of partially‐filled rubber mixing in a 2‐wing rotor‐equipped chamber. Journal of Applied Polymer Science. 2016; 134(2). doi: 10.1002/app.44250 DOI: https://doi.org/10.1002/app.44250
20. Gaspar-Cunha A, Covas JA. The Plasticating Sequence in Barrier Extrusion Screws Part II: Experimental Assessment. Polymer-Plastics Technology and Engineering. 2014; 53(14): 1456-1466. doi: 10.1080/03602559.2014.909482 DOI: https://doi.org/10.1080/03602559.2014.909482
21. Zitzenbacher G, Karlbauer R, Thiel H. A New Calculation Model and Optimization Method for Maddock Mixers in Single Screw Plasticising Technology. International Polymer Processing. 2007; 22(1): 73-81. doi: 10.3139/217.0109 DOI: https://doi.org/10.3139/217.0109
22. Dörner M, Marschik C, Schöppner V, et al. Development of an Analytical Model to Describe the Disperse Melting in Wave-Dispersion Screws. Polymers. 2020; 12(4): 946. doi: 10.3390/polym12040946 DOI: https://doi.org/10.3390/polym12040946
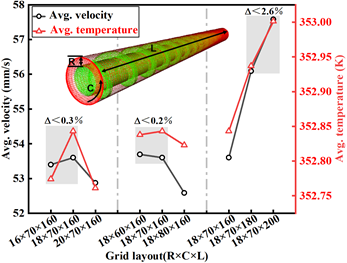
Downloads
Published
How to Cite
Issue
Section
License
Copyright (c) 2024 Wei Pan, Shizheng Huang, Jiawei Zhu, Xiankui Zeng, Weimin Yang, Ranran Jian

This work is licensed under a Creative Commons Attribution 4.0 International License.